David Dreyer, Undergraduate Researcher
David Dreyer is majoring in Aerospace Engineering with a minor in Physics and is set to graduate in Fall 2025. Dreyer first became involved in research through the Summer Undergraduate Research Experience (SURE) program for SURE 2023 after Dr. Ali Abdul-Aziz approached him with a research opportunity. Dr. Aziz encouraged Dryer to select a topic to research, and Dreyer decided to focus on 3D printing and how wall thickness, infill density, and print pattern contribute to tensile strength. This research idea culminated in Dreyer’s project “Material Testing of Fused Deposition Modeling (FDM) Using Printed Part Applications.” Dreyer went on to win the Three Minute Thesis competition for SURE 2023, which is an event that challenges all SURE participants to present their research in a three-minute time frame, but his work didn’t stop there. Dreyer continued his research during SURE 2024 and remains active in research throughout the academic year.
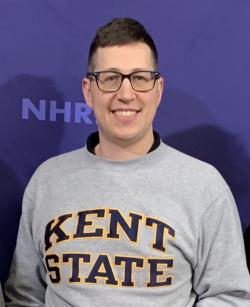
The inspiration for Dreyer’s research on 3D printing stemmed from the limited amount of information that is currently available. After some digging, Dreyer realized that no research had been done on the relationship between the tensile strength of a 3D printed object and variables within the printing process. To formulate a research concept, Dreyer focused on three main aspects of 3D printing: wall thickness, infill density, and print pattern. By focusing on wall thickness, infill density, and print pattern, Dreyer was able to explore the relationship between the components of 3D printing and the strength of a specimen.
Dreyer explained that “if you’re in aerospace, weight is important,” so a major goal of his research is to be able to “make a [specimen] lighter while meeting the same strength requirements.” Wall thickness is a significant contributor to the weight of a 3D printed object, so adjusting the wall thickness can greatly reduce the weight. Infill density is another major contributor to weight. A majority of 3D printed objects have infill percentages of about 20%. The specimens that Dreyer has been testing have infill ranges from 10-30%. The infill density itself is influenced by the print pattern. Print patterns can be square, triangular, 2D, and 3D. Dreyer explained that for an object with a 3D print pattern, “as the layers go up, the print pattern changes orientation to create a 3D effect on the inside.” Through testing, Dreyer has discovered that the 3D print pattern “gives a lot more strength for the same weight” when compared to other patterns.
All three variables require extensive testing, and with each adjustment to a variable, Dreyer would print another specimen. Dreyer noted that he’s worked with approximately 300 specimens throughout his research. Each individual specimen has to be tested, but before testing can occur, the specimen must first be printed. Dreyer’s research utilizes PLA to print the specimens, which is a common and readily available 3D printing filament. PLA isn’t an aerospace-suited printing filament, but Dreyer’s research “isn’t as much about material as it is about the way the material reacts with the way it’s printed.” Dreyer is optimistic that the results he produced through the PLA specimens will be comparable to what can be expected from other printing materials.
Although it seems straightforward, Dreyer explained that “3D printing is never smooth.” Issues can arise, and even the smallest discrepancy or an error in a print would require the specimen to be scrapped to preserve the integrity of the experiment. Only once a specimen is deemed properly printed does it move onto testing.
In order to evaluate the specimens, Dreyer relies on two pieces of technology. The first is a tensile tester, which gives the raw breaking strength of the specimen, and the other is the Dantec Dynamics DIC system, which is a system used by NASA. The system incorporates a set of hypersensitive cameras and software that allows the strain on the specimen to be tracked throughout the entire test. The system lets users see localized strain and how the specimen reacts, effectively allowing Dreyer to see where the specimen will break before it does.
The Dantec Dynamics DIC system is technology not readily available to most, so Dreyer was ecstatic at the opportunity to use and learn the complex system. Learning the intricacies of new technology is what Dreyer revealed to be the most challenging part of his research, stating that “half the SURE program was just getting familiar with the equipment because it’s so technical and involved.” Despite the challenge of adapting to the new technology, Dreyer expressed his gratitude for the chance to work with such specialized technology.
When asked about the application of his research, Dreyer explained that his work will “lead to more future research” by providing “a general idea of how [researchers] can expect materials to react in certain scenarios based on how [researchers] print them.” Dreyer’s research has paved the way for revolutionizing the usage of 3D printed parts, especially in aerospace engineering. Dreyer stressed that “every gram counts when you’re putting stuff into space,” and that “if you can save half the weight on a part by making it hollow—as long as it meets the strength requirements—that’s golden.”
Undergraduate student research has been a major component of Dreyer’s academic career at 91˛Öżâ, and when asked if he recommends that other students participate in research, Dreyer was quick to reply, saying “Oh, 100%.”
Undergraduate research boosts academics and provides a great foundation for a career, and Dreyer reflected that concept by saying “it’s one thing to graduate by going in the classroom and getting a degree, but it’s a whole other world to have these experiences.” Dreyer’s experiences with undergraduate student research impacted him far beyond the academic and research setting. The experience that Dreyer has with complex technology sets him apart from others in his field and makes him highly desirable to future employers. Beyond the resume-building experience with technology, Dreyer also gained critical communication skills. The research setting pushed Dreyer out of his comfort zone and taught him how to adopt a “real-world mindset.” Dreyer explained that “learning the equipment and the social side of [research]” are the biggest takeaways from his experience.
Dreyer gave a special thanks to his research mentor Dr. Aziz, and to Ann Gosky, the director of the SURE program, for their continued support. Dreyer emphasized that his research “wouldn’t be possible without the people who support the program.”
Written by Lenore Kohl